Resumes
Resumes
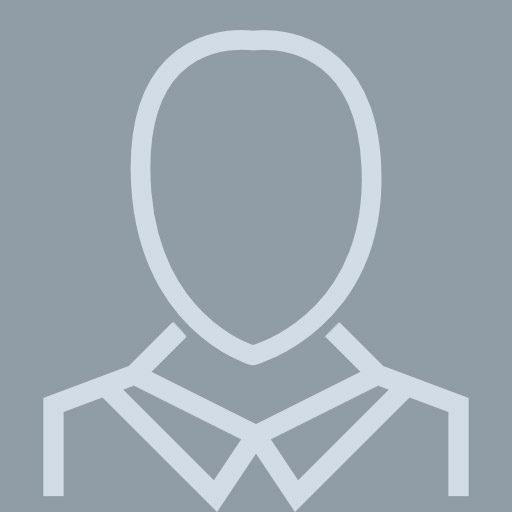
Senior Vision System Engineer
View pageLocation:
4106 70Th Street Cir east #east, Palmetto, FL 34221
Industry:
Machinery
Work:
Bucher Emhart Glass
Senior Vision System Engineer
Senior Vision System Engineer
Education:
Science College, Matale
University of Peradeniya
The Ohio State University
University of Peradeniya
The Ohio State University
Skills:
Engineering
Automation
Manufacturing
Product Development
Continuous Improvement
Process Improvement
Engineering Management
Strategic Planning
Project Management
Lean Manufacturing
Science
Cross Functional Team Leadership
Root Cause Analysis
Design For Manufacturing
Heat Transfer
Industrial Engineering
Machine Vision
Solidworks
Manufacturing Engineering
Team Leadership
Electronics
Programming
5S
Automation
Manufacturing
Product Development
Continuous Improvement
Process Improvement
Engineering Management
Strategic Planning
Project Management
Lean Manufacturing
Science
Cross Functional Team Leadership
Root Cause Analysis
Design For Manufacturing
Heat Transfer
Industrial Engineering
Machine Vision
Solidworks
Manufacturing Engineering
Team Leadership
Electronics
Programming
5S
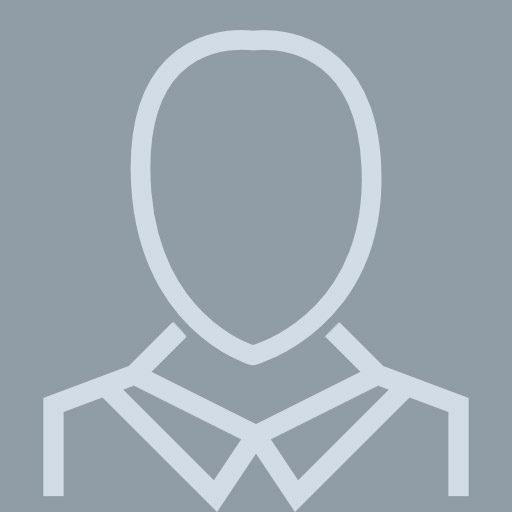