Resumes
Resumes
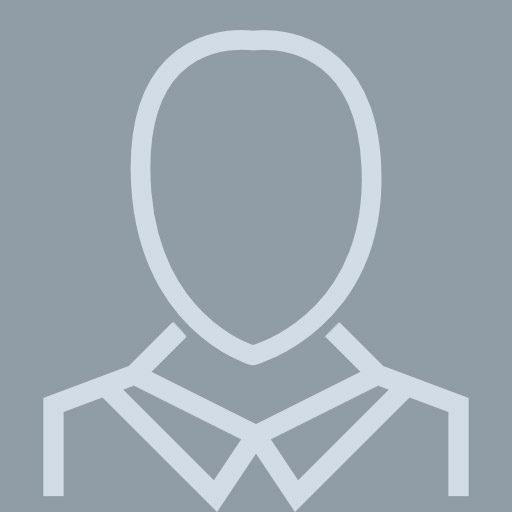
Staff Engineer
View pageLocation:
San Antonio, TX
Industry:
Medical Devices
Work:
Southwest Research Institute
Staff Engineer
Staff Engineer
Education:
The University of Texas at Austin 1989 - 1993
Doctorates, Doctor of Philosophy, Electrical Engineering The University of Texas at Austin 1987 - 1988
Master of Science, Masters, Electrical Engineering Trinity University 1982 - 1986
Bachelors, Bachelor of Science, Engineering Southwest Research Institute
Edison High School
Doctorates, Doctor of Philosophy, Electrical Engineering The University of Texas at Austin 1987 - 1988
Master of Science, Masters, Electrical Engineering Trinity University 1982 - 1986
Bachelors, Bachelor of Science, Engineering Southwest Research Institute
Edison High School
Skills:
Biomedical Engineering
R&D
Medical Devices
Labview
Signal Processing
Matlab
Engineering Management
Image Processing
Design of Experiments
Program Management
Systems Engineering
Simulations
Algorithms
Iso 13485
Embedded Systems
Sensors
Electronics
Optics
R&D
Medical Devices
Labview
Signal Processing
Matlab
Engineering Management
Image Processing
Design of Experiments
Program Management
Systems Engineering
Simulations
Algorithms
Iso 13485
Embedded Systems
Sensors
Electronics
Optics
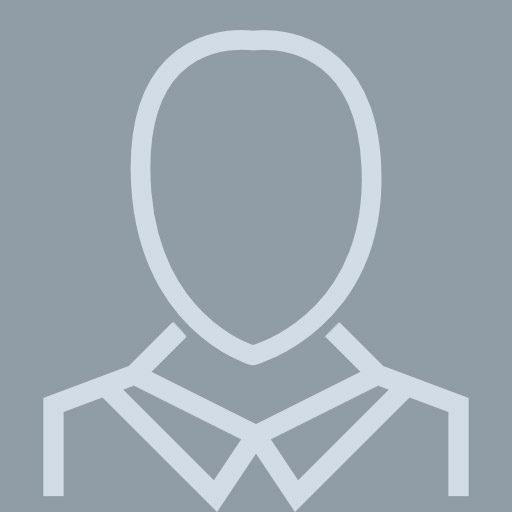
Keith Bartels
View page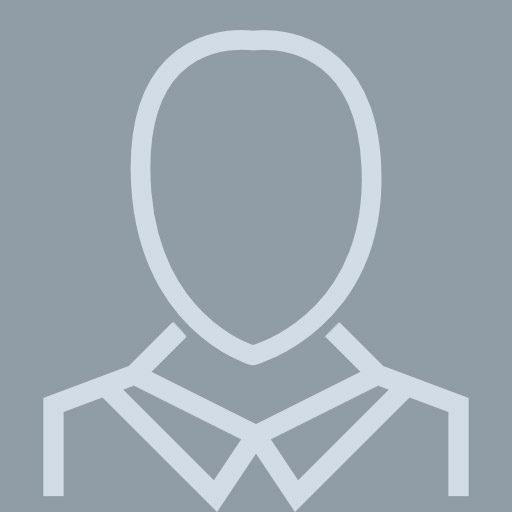
Keith Bartels
View pageLocation:
United States