Resumes
Resumes
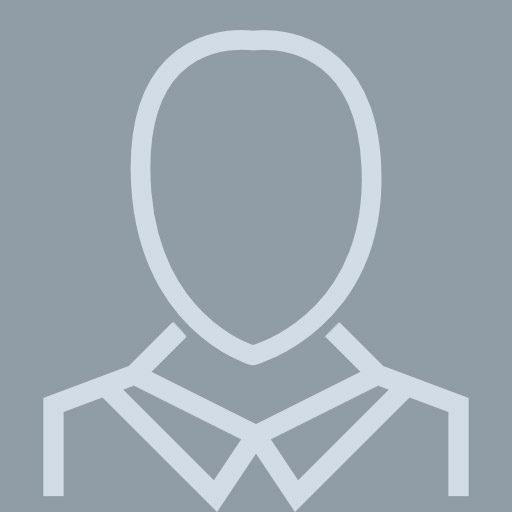
Chief Metallurgist
View pageLocation:
Stow, OH
Industry:
Program Development
Work:
Energy Industries of Ohio
Chief Metallurgist
Babcock & Wilcox Jun 1972 - Jun 2014
Manager of Materials and Manufacturing Technology
Chief Metallurgist
Babcock & Wilcox Jun 1972 - Jun 2014
Manager of Materials and Manufacturing Technology