Resumes
Resumes
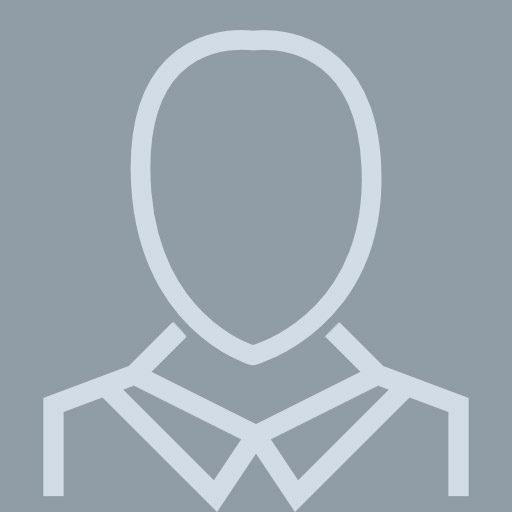
President
View pageLocation:
Fort Wayne, IN
Industry:
Mining & Metals
Work:
Horace Pops Consulting
President
President
Education:
University of Pittsburgh 1958 - 1962
Doctorates, Doctor of Philosophy, Philosophy Lehigh University 1957 - 1958
Masters Rensselaer Polytechnic Institute 1954 - 1957
Bachelors
Doctorates, Doctor of Philosophy, Philosophy Lehigh University 1957 - 1958
Masters Rensselaer Polytechnic Institute 1954 - 1957
Bachelors
Skills:
Six Sigma
Quality Management
Team Building
Lean Manufacturing
Purchasing
Extrusion
Manufacturing Engineering
Root Cause Analysis
Iso
Metallurgy
5S
Metals
Supply Chain Management
Negotiation
Process Improvement
Steel
Engineering
Strategic Planning
Materials
Sales Management
Operations Management
New Business Development
Cross Functional Team Leadership
Manufacturing
Value Stream Mapping
Manufacturing Operations Management
Contract Negotiation
Budgets
Business Strategy
Product Development
Kaizen
Process Engineering
Spc
Marketing Strategy
Continuous Improvement
Quality Management
Team Building
Lean Manufacturing
Purchasing
Extrusion
Manufacturing Engineering
Root Cause Analysis
Iso
Metallurgy
5S
Metals
Supply Chain Management
Negotiation
Process Improvement
Steel
Engineering
Strategic Planning
Materials
Sales Management
Operations Management
New Business Development
Cross Functional Team Leadership
Manufacturing
Value Stream Mapping
Manufacturing Operations Management
Contract Negotiation
Budgets
Business Strategy
Product Development
Kaizen
Process Engineering
Spc
Marketing Strategy
Continuous Improvement