Resumes
Resumes
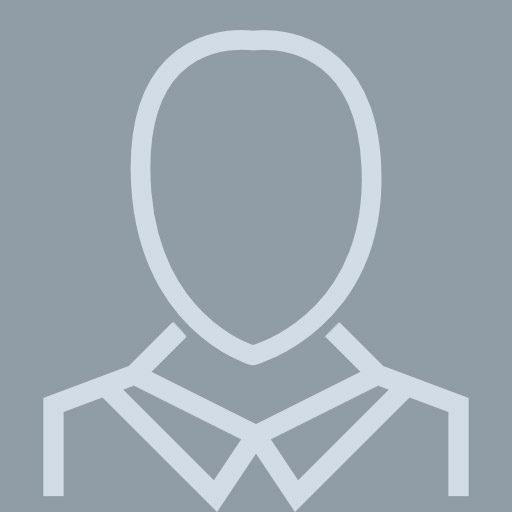
Consulting Software Engineer
View pageLocation:
318 Seaboard Ln, Franklin, TN 37067
Industry:
Computer Software
Work:
Cognex Corporation 2005 - 2017
Principal Engineer at Cognex Corporation
Cognex Corporation 2005 - 2017
Consulting Software Engineer
Automated Vision 1998 - 2005
Scientist
Principal Engineer at Cognex Corporation
Cognex Corporation 2005 - 2017
Consulting Software Engineer
Automated Vision 1998 - 2005
Scientist
Education:
University of Louisiana at Lafayette 1994 - 1998
Doctorates, Doctor of Philosophy, Computer Engineering Indian Institute of Technology, Madras 1991 - 1993
R. V. College of Engineering, Bangalore 1987 - 1991
Bachelor of Engineering, Bachelors
Doctorates, Doctor of Philosophy, Computer Engineering Indian Institute of Technology, Madras 1991 - 1993
R. V. College of Engineering, Bangalore 1987 - 1991
Bachelor of Engineering, Bachelors
Skills:
Image Processing
Algorithms
Computer Vision
Object Oriented Design
Software Engineering
Machine Vision
Signal Processing
C++
C
Digital Signal Processors
Software Development
Pattern Recognition
Dsp
Qt
Algorithms
Computer Vision
Object Oriented Design
Software Engineering
Machine Vision
Signal Processing
C++
C
Digital Signal Processors
Software Development
Pattern Recognition
Dsp
Qt