Resumes
Resumes
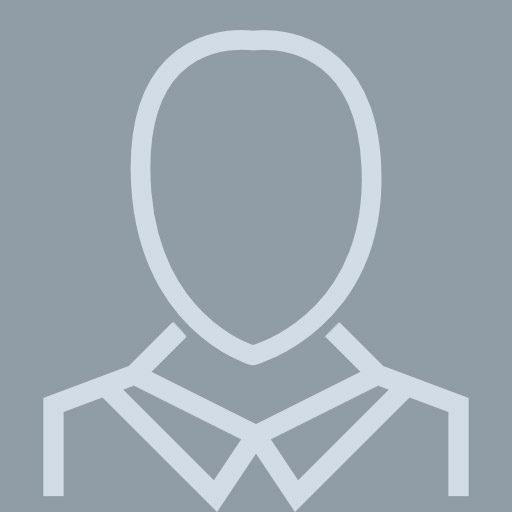
Staff Researcher
View pageLocation:
Warren, MI
Industry:
Automotive
Work:
General Motors - Warren, MI since Feb 2012
Senior Manufacturing Project Engineer
General Motors - Warren, MI since Feb 2010
Senior Researcher
General Motors - Warren, MI Jan 2006 - Jan 2010
Researcher
Senior Manufacturing Project Engineer
General Motors - Warren, MI since Feb 2010
Senior Researcher
General Motors - Warren, MI Jan 2006 - Jan 2010
Researcher
Education:
Georgia Institute of Technology 2000 - 2005
Doctor of Philosophy (Ph.D.), Mechanical Engineering Georgia Institute of Technology 2001 - 2003
Master of Science (M.S.), Electrical and Computer Engineering Georgia Institute of Technology 2000 - 2002
Master of Science in Mechanical Engineering (M.S.M.E.), Mechanical Engineering Tsinghua University 1996 - 1999
Bachelor of Engineering (B.E.), Industrial Engineering Tsinghua University 1994 - 1999
Bachelor of Engineering (B.E.), Mechanical Engineering
Doctor of Philosophy (Ph.D.), Mechanical Engineering Georgia Institute of Technology 2001 - 2003
Master of Science (M.S.), Electrical and Computer Engineering Georgia Institute of Technology 2000 - 2002
Master of Science in Mechanical Engineering (M.S.M.E.), Mechanical Engineering Tsinghua University 1996 - 1999
Bachelor of Engineering (B.E.), Industrial Engineering Tsinghua University 1994 - 1999
Bachelor of Engineering (B.E.), Mechanical Engineering
Skills:
Robotics
Simulations
Simulink
Matlab
Manufacturing
Optimization
Dynamics
Engineering
Automotive Engineering
Design of Experiments
Fmea
Automotive
Controls
Safety
Control Theory
Modeling
Internal Controls
Powertrain
Manufacturing Engineering
Engineering Management
Lean Manufacturing
Failure Mode and Effects Analysis
Simulations
Simulink
Matlab
Manufacturing
Optimization
Dynamics
Engineering
Automotive Engineering
Design of Experiments
Fmea
Automotive
Controls
Safety
Control Theory
Modeling
Internal Controls
Powertrain
Manufacturing Engineering
Engineering Management
Lean Manufacturing
Failure Mode and Effects Analysis