Resumes
Resumes
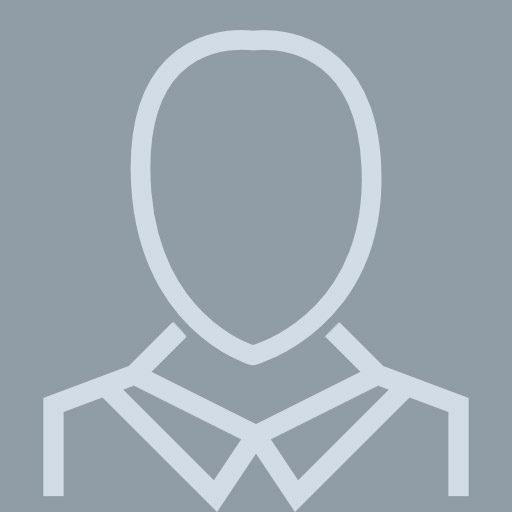
Lead System Engineer
View pageLocation:
Phoenix, AZ
Industry:
Aviation & Aerospace
Work:
Honeywell
Manager Project Engineering
Honeywell Jan 1982 - Jan 2012
Principal Engineer
Honeywell Aerospace Jan 1982 - Jan 2012
Lead System Engineer
Manager Project Engineering
Honeywell Jan 1982 - Jan 2012
Principal Engineer
Honeywell Aerospace Jan 1982 - Jan 2012
Lead System Engineer
Education:
Northern Arizona University 1978 - 1981
Bachelor of Science In Mechanical Engineering, Bachelors
Bachelor of Science In Mechanical Engineering, Bachelors
Skills:
Engineering Management
Aerospace
Systems Engineering
Six Sigma
Avionics
Earned Value Management
Do 178B
Engineering
Mechanical Engineering
Root Cause Analysis
Space Systems
Testing
Aerospace Engineering
Project Management
Manufacturing Engineering
Manufacturing
Program Management
Lean Manufacturing
Green Belt
Telelogic Doors
System Design
Continuous Improvement
Spacecraft
Satellite Systems Engineering
Flight Test
Value Stream Mapping
Aircraft
Simulations
Arinc 429
Kaizen
Composites
Finite Element Analysis
Process Improvement
Requirements Management
Systems Design
Ms Project
Design For Manufacturing
Sensors
Fmea
Aerospace
Systems Engineering
Six Sigma
Avionics
Earned Value Management
Do 178B
Engineering
Mechanical Engineering
Root Cause Analysis
Space Systems
Testing
Aerospace Engineering
Project Management
Manufacturing Engineering
Manufacturing
Program Management
Lean Manufacturing
Green Belt
Telelogic Doors
System Design
Continuous Improvement
Spacecraft
Satellite Systems Engineering
Flight Test
Value Stream Mapping
Aircraft
Simulations
Arinc 429
Kaizen
Composites
Finite Element Analysis
Process Improvement
Requirements Management
Systems Design
Ms Project
Design For Manufacturing
Sensors
Fmea