Resumes
Resumes
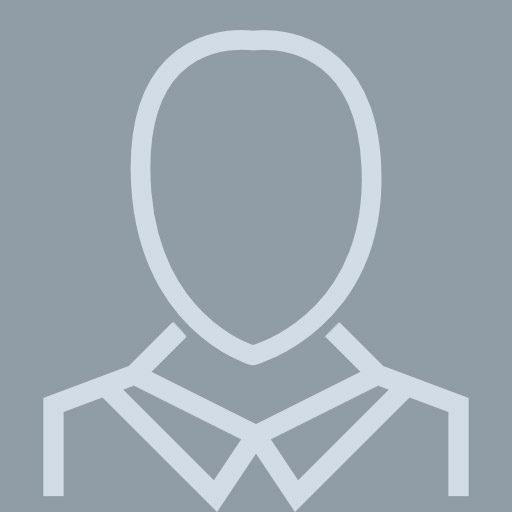
Avish Bharwani
View pageLocation:
3460 Bella Vista Ct, Santa Clara, CA 95051
Industry:
Industrial Automation
Work:
Kawasaki Robotics USA inc. - San Jose, CA since Aug 2011
Manager, Sales
Kawasaki Robotics USA inc. Jun 2009 - Aug 2011
Account Manager
Kawasaki Robotics USA inc. Aug 2006 - Jun 2009
Robotics Engineer
Manager, Sales
Kawasaki Robotics USA inc. Jun 2009 - Aug 2011
Account Manager
Kawasaki Robotics USA inc. Aug 2006 - Jun 2009
Robotics Engineer
Education:
San Francisco State University 2001 - 2005
Bachelor of Science (BS), Electrical and Electronics Engineering
Bachelor of Science (BS), Electrical and Electronics Engineering
Skills:
Engineering Management
Robotics
Cross Functional Team Leadership
Engineering
Automation
Product Development
Mechatronics
Management
Project Management
Design of Experiments
Program Management
Robotics
Cross Functional Team Leadership
Engineering
Automation
Product Development
Mechatronics
Management
Project Management
Design of Experiments
Program Management
Languages:
English
Japanese
Sindhi
Japanese
Sindhi